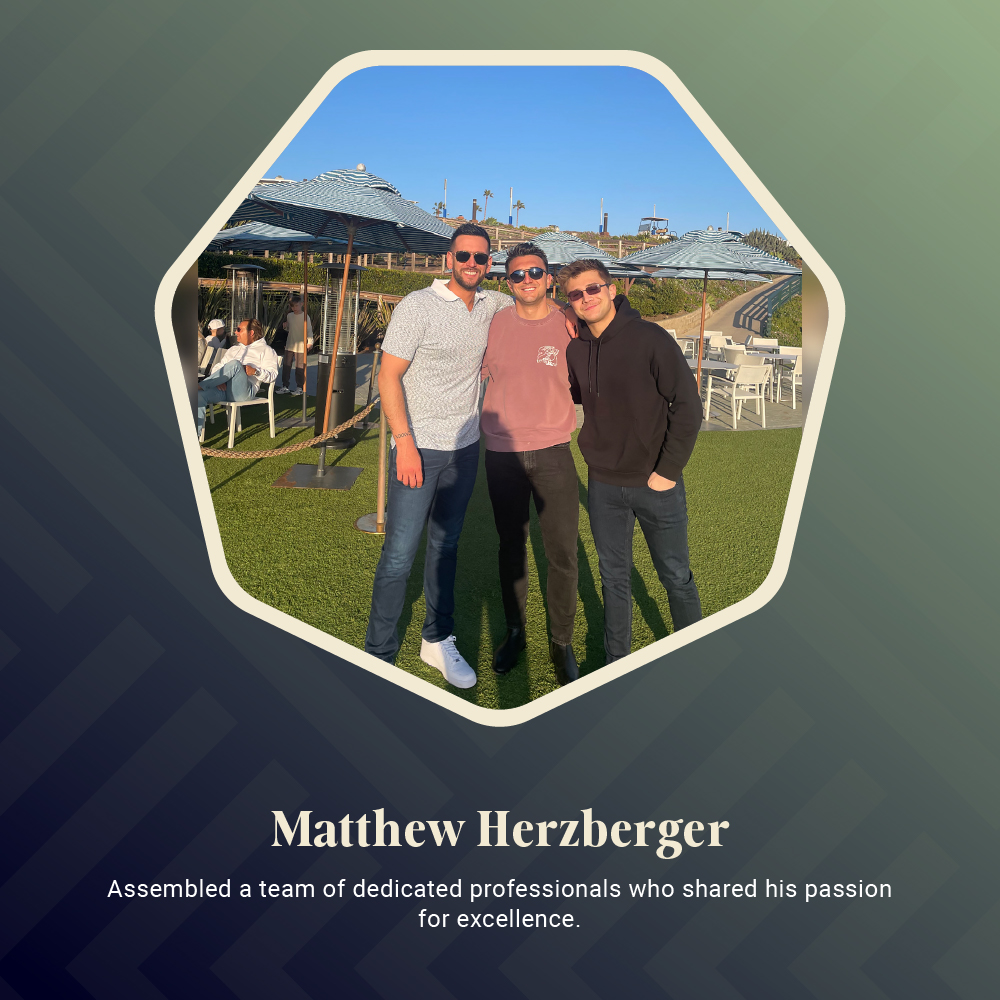
Efficient warehouse operations are critical for businesses to meet demand, minimize costs, and maintain high levels of customer satisfaction. Whether you’re a small retailer or a large logistics company, optimizing your warehouse can lead to better productivity, reduced overhead, and improved safety. This guide will walk you through essential strategies to streamline your warehouse operations effectively.
Optimizing Layout and Space Utilization
One of the first steps to improving warehouse efficiency is optimizing the physical layout. A well-designed warehouse leads to wasted time and resources as workers spend more time navigating the facility.
Maximize Vertical Space
Rather than expanding the warehouse floor, consider utilizing vertical storage. Invest in high-quality shelving and racking systems that allow you to store items upwards. This not only saves space but also allows for quicker retrieval times since items can be organized based on frequency of use or product categories.
Implement Zoning
Zoning helps streamline the workflow by grouping similar items in logical sections of the warehouse. For example, fast-moving products should be stored near shipping areas, while slow-moving items can be kept further away. This reduces unnecessary travel time and improves overall operational speed.
Embrace Technology for Automation
Automation is a powerful tool for optimizing warehouse operations. Technological advancements, from robots to AI-driven software, can help reduce human error, improve accuracy, and increase throughput.
Warehouse Management Systems (WMS)
A robust Warehouse Management System (WMS) integrates various processes such as inventory management, order picking, and tracking. WMS solutions offer real-time data, making it easier to monitor stock levels, reduce overstocking, and accurately predict future demand.
Automated Picking Systems
Automated picking technologies, such as robotic arms and conveyor belts, can significantly reduce the time it takes to pick and pack items. Systems also minimize the potential for human error, ensuring more accurate order fulfillment.
Improve Inventory Management
Effective inventory management is critical to reducing waste, lowering holding costs, and ensuring products are available when needed.
Use the ABC Analysis
The ABC analysis classifies inventory based on its value and importance. Items are divided into three categories:
- A (high-value, low-quantity)
- B (moderate value and quantity)
- C (low-value, high-quantity)
This system helps prioritize stock levels for the most critical products, ensuring that high-demand items are always available.
Implement Cycle Counting
Cycle counting involves counting a small subset of inventory on a regular basis rather than conducting a full inventory audit once a year. This allows for continuous inventory accuracy, helps identify discrepancies early, and ensures that records are always up to date.
Enhance Labor Efficiency
The human element is one of the most critical factors in warehouse operations. Efficient labor management can significantly impact productivity, safety, and overall performance.
Cross-Training Employees
Cross-training employees to handle various roles within the warehouse ensures flexibility. If someone is absent or a specific area experiences a high workload, other staff members can step in seamlessly. This minimizes downtime and keeps the workflow smooth.
Use Labor Management Software
Labor management software helps monitor employee productivity, track hours worked, and assign tasks more effectively. It can also identify bottlenecks and areas for improvement, enabling better labor allocation and ensuring that workers are used efficiently.
Prioritize Safety and Compliance
A safe warehouse is an efficient warehouse. Accidents, injuries, and non-compliance can cause disruptions and increase costs.
Regular Safety Audits
Conduct regular safety audits to identify potential hazards, such as poorly maintained equipment or obstructed pathways. Ensure that all safety protocols are being followed, and provide ongoing safety training to all employees.
Invest in Personal Protective Equipment (PPE)
Providing employees with the necessary protective gear, such as gloves, helmets, and high-visibility clothing, reduces the risk of injury. Make sure that all safety equipment is easily accessible and well-maintained.
Monitor and Measure Key Performance Indicators (KPIs)
Tracking warehouse performance through Key Performance Indicators (KPIs) enables continuous improvement and helps identify areas that need attention.
Order Accuracy Rate
The order accuracy rate measures how often orders are fulfilled without error. A high accuracy rate leads to greater customer satisfaction, fewer returns, and reduced operational costs. Monitoring this KPI can help identify gaps in the picking, packing, or shipping processes.
Inventory Turnover Rate
This KPI tracks how often inventory is sold and replaced over a specific period. A higher turnover rate indicates efficient stock management, while a low rate may suggest overstocking or issues with product demand forecasting.
Leverage Data for Continuous Improvement
Data-driven decision-making is the cornerstone of successful warehouse management. Analyzing historical data can provide insights into patterns, inefficiencies, and opportunities for improvement.
Use Predictive Analytics
Predictive analytics tools can forecast demand based on past trends, helping you optimize stock levels and labor allocation. This prevents understocking or overstocking and ensures that resources are used efficiently.
Implement Real-Time Monitoring
Real-time data monitoring allows managers to identify and resolve issues immediately. For example, if a conveyor belt fails, real-time alerts enable quick responses, reducing downtime and avoiding bottlenecks in the workflow.
The Path to Efficient Warehouse Operations
Effective warehouse management involves a combination of intelligent planning, embracing technology, optimizing labor, and ensuring safety. By focusing on these critical areas, businesses can significantly improve their operational efficiency, reduce costs, and enhance customer satisfaction. Keeping up with technological trends and continuously refining processes will ensure that your warehouse remains competitive and capable of meeting future challenges.